100 years have passed since the development of the first concrete products, but until now this building material has not lost its relevance, and the products are being modified every year. The main advantages of a concrete slab are long service life under various conditions without loss of qualities, as well as the ability to resist corrosion and decay. Therefore, slabs are used not only for construction, but also for laying roads, installing engineering networks.
Content
Production, composition and scope of concrete floor slabs and other types of products
Building slabs are manufactured in specialized enterprises or factories that produce reinforced concrete products. The assortment of goods is often represented not only by various types of floors, but also by other products, including:
- piles;
- blocks and pillows for the foundation;
- flights of stairs;
- paving slabs;
- Wall panels.
The properties and characteristics of concrete products depend on the type of construction, the quality of the concrete mixture and other materials used, and most importantly, on compliance with the production technology. Basically, the technical parameters of the goods depend on the properties of two main constituent elements:
- concrete;
- steel reinforcing parts.
It is interesting! Concrete itself is considered to be quite fragile, its main advantage is resistance to corrosion. Steel is a material that degrades when exposed to moisture. However, when combined, these two elements form a perfect tandem, because steel increases the strength of concrete, and concrete, in turn, protects steel from rust and corrosion.
Depending on the type of product, the grade of steel reinforcement and concrete used is selected, as well as the number of reinforcement layers, wire diameter and mesh spacing. The more reinforcement was used, the higher the strength characteristics of the final product.To strengthen floor slabs or other products, certain types of reinforcement are used, the designation of which is contained in the labeling of each product:
- Вр-II - high-strength wire;
- A-IV, A-V, A-VI - hot-rolled bar;
- At-IV, At-VI, At-V - a bar characterized by increased strength;
- K-7 is a reinforcing rope with the best strength characteristics.
The features of production include the following points:
- A foundation concrete slab has a larger cross-section compared to conventional floor slabs.
- Multidirectional laying of the reinforcing profile improves the load properties of the products, especially the bending load.
- To prevent cracking at the support points, a reinforced support belt is laid around the perimeter of the slabs.
- For more convenient transportation and laying, lifting eyes are mounted on the surface of the slabs.
The strength of the finished products depends on the type of concrete used. Usually, a concrete mixture M-200 or M-300 is used, having a strength class of at least B-22.5. In the case of using special types of concrete, additional marking is applied: cellular concrete - I, heat-resistant - Zh, porous - P. The following types of slabs are used on private and industrial construction sites:
- overlapping;
- foundation;
- interior or exterior wall panels;
- cover plates.
It is these types of concrete products that form the basis of the building frame. In addition, paving and road concrete slabs are produced. Concrete products used to create fences and other fences can be distinguished into a separate group.
Pros and cons of using concrete floor slabs and other concrete products
Not a single construction can be imagined without the use of reinforced concrete products, because, first of all, they are distinguished by an affordable price and wide distribution. Another significant advantage is the fact that some types of slabs can be made independently, since the basis of concrete is water and cement, and scrap of ferrous metal can be used as reinforcement. It should be borne in mind that it will be difficult to determine the load capacity of independently made elements. For production, it is better to hire a specialist who will monitor the manufacturing process.

The large weight of the product requires the use of special equipment during installation and transportation
Other advantages of concrete slabs are:
- Easy product availability. Plants for the production of reinforced concrete panels are located in almost every city.
- Standard sizes. The dimensions of the slabs, like other parameters, are clearly regulated by the standards of GOST, which allows you to calculate the exact number of products that will be needed during construction. Moreover, the slabs are distinguished by a wide variety of dimensions.
- Higher speed of work. Laying floor slabs makes it possible to significantly reduce the time spent on work.
- Long service life. Wooden beams are sometimes used as interfloor floors, but a house made of concrete slabs will not only be stronger, but also more durable.
- Improved consumer properties. Due to the features of production, which are constantly being improved, the use of concrete slabs helps to improve the sound and thermal insulation of the finished building or engineering communications. Also, slabs provide additional fire safety, because concrete is a non-combustible material.
- Smooth surface. Floor slabs are characterized by a flat surface that is easier to process during the interior finishing stage, which makes the product attractive for residential construction.
It is interesting! Additional advantages of concrete products are considered to be high indicators of resistance to vibrations, which makes it possible to use them in the construction of industrial facilities, and also makes it possible to erect buildings in an area of increased seismic activity.
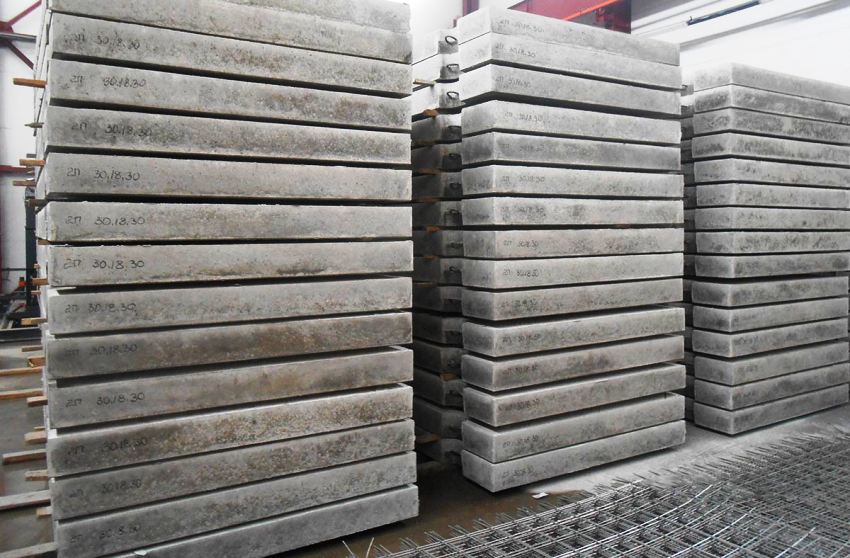
An important advantage of concrete slabs is the reliability of the structure and their long service life.
Despite the large number of advantages, the following disadvantages can be distinguished in the use of concrete products:
- Great weight. Due to the significant mass of slabs during construction, it is required to use additional lifting equipment, which is especially difficult when erecting high-rise buildings.
- Shipping costs. As for floor slabs, they are often characterized by a large volume, which does not allow bringing the required number of slabs at one time for the construction of a private house from reinforced concrete panels.
- The need for accurate calculations. Before starting construction, you need to correctly determine the future load on the floors and, based on it, purchase certain types of panels.
Concrete slab: types of products, their distinctive features
Various types of concrete slabs differ among themselves in terms of design, shape, purpose, method of operation, as well as surface texture. The final cost of a concrete slab is influenced by the following parameters:
- the brand of concrete used. It can be light, heavy or silicate material;
- features of the internal structure. The slab can be characterized by the presence of through channels (hollow-hollow structures) or be monolithic, that is, solid or solid;
- product parameters. In accordance with the standards of GOST, the products have standard indicators of length, thickness and width. However, monolithic structures can be not only standard, but also made according to individual parameters;
- installation method depending on the depth of support of the floor slabs on the walls. Console panels require two points of support and are used for the construction of outriggers - balconies or canopies. Beam floors are installed with two, three or four supports;
- section profile. Concrete products can be of the correct geometric shape, for example, rectangular or square, as well as beveled or have ribs;
- method and technology of production. One-piece seamless options or prefabricated structures are distinguished, which are made by vibration, injection molding or continuous molding;
- type of reinforcement. Concrete products can be conventional unstressed or prestressed;
- type of binder. The production of panels can be based on cement, gypsum or silicate-concrete mixture.
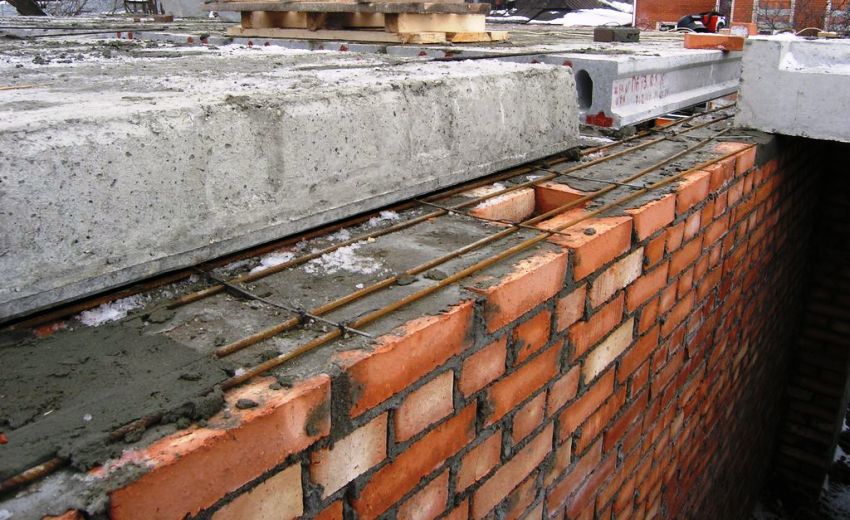
In accordance with GOST standards, the slabs have standard indicators of length, thickness and width
What are monolithic reinforced concrete floor slabs
Monolithic floor slabs are used mainly for creating interfloor partitions and organizing heating mains. Manufacturing technology is regulated by the GOST 12767-94 normative act. Due to the absence of joints and seams, monolithic structures are characterized by increased strength characteristics and are used for both residential and industrial construction.
Depending on the manufacturing method, solid slabs are contoured, requiring the presence of supports along the entire contour of the slab, as well as three- and two-sided. The main difference between a monolith and another type of concrete products is the greatest weight, which on average reaches 300 kg per square meter of floor. For this reason, solid slabs are often cast directly at the construction site in demountable contours that can even be rented. This saves time and money in transporting, loading and unloading panels.
Monolithic slabs, again due to the peculiarities of manufacturing, are characterized by good water and frost-resistant properties, which plays a significant role in the operation of the finished building.Customers also show increased requirements for the appearance of products, because their surface should be perfectly flat, without sagging and protruding ends of steel reinforcement.
Important! The main disadvantage of the monolith is the long solidification period. In accordance with the norms, a monolithic slab is considered completely solidified only 28 days after pouring, and a house made of reinforced concrete slabs will shrink for a long time.
As for the dimensions of solid slabs, in this case there are both standard and other sizes. The thickness of the monolith is selected taking into account the maximum longitudinal distance between the supports. So, with a non-girder type of structure, the height of the monolith is determined by the ratio of 1:30, but in any case, it is not recommended to use a slab whose thickness is less than 15 cm. In calculating floor slabs, these indicators are considered the most important, affecting the load capacity of products. If a span of more than 6 meters is required, regardless of the thickness of the slab, additional reinforcement is required.
How much does a concrete slab cost? The selected reinforcement scheme and the height of the slab affect the cost of products. On average, the price of filling varies from 1,500 to 9,000 rubles per cubic meter.

Monolithic slabs are used in the construction of massive structures, heating mains, external structures
Hollow-core floor slabs: GOST, dimensions and features of the use of structures
The hollow-core series of floor slabs has been popular for many years due to the fact that the panels are characterized by increased strength characteristics, but at the same time they have less weight, in contrast to the monolithic type of floors.
Related article:
Reinforced concrete blocks: a universal material for the construction of reliable buildings
Scope of use. Varieties of blocks by type, size and area of application. The procedure for installing reinforced concrete blocks.
In the production of hollow-type reinforced concrete slabs (PKZH), heavy concrete is mainly used, and inside each part there are through channels or voids concreted from the ends. In both cases, there are air chambers inside the slab, thanks to which hollow-core panels receive the following advantages:
- Less consumption of concrete during production, which affects the lower price of reinforced concrete slabs.
- Simplification of the laying of communications. The voids allow you to organize not only electricity and water supply networks, but also other communications.
- Less pressure on the foundation. The presence of voids significantly reduces the weight of the products, and, accordingly, the entire structure, and therefore the pressure on the base of the structure decreases.
- Short construction times and no shrinkage. The slabs are delivered ready for installation, which allows continuous construction without waiting times.
Important! If the through outlets of the channels are open at the end, you should close the holes yourself, using a cement mixture and some kind of insulation material.

Hollow core slabs weigh significantly less than other products and therefore create less stress on the foundation of the building
The disadvantages of PKZH slabs include only lower strength (compared to monolith) and the presence of joints. In general, the use of hollow-core slabs has a positive effect on the sound and thermal insulation of the building. According to GOST standards, the plates differ in the following characteristics:
- Thickness. In most cases, the height of the slabs reaches 22 cm, but there is a lighter type of hollow products, the thickness of which is 16 cm, and there are also products of increased strength with a height of 30 cm.
- Width. The most common are slabs with a width of 1, 1.2, 1.5, very rarely products with a size of 1.8 are found.
- Length.The indicator depends on the manufacturing method, for example, concrete products produced using formwork have a length from 2380 mm to 8980 mm. The length of the non-formwork options can reach 12 meters in the case of an individual order, while the slab can be cut into elements of any length with an accuracy of 10 cm.
- The nominal distance between the channels of the floor slab. The average distance between the centers of the voids is 185 mm; at least 26 mm should remain between the edges of the channels.
- Internal hole diameter. The indicator varies from 114 to 203 mm.
Characteristics of ribbed or U-shaped floor slabs, roof panels and wall slabs
If you look at the drawing of floor slabs of this type, the special shape of the products is immediately striking. It is because of the unusual configuration that ribbed slabs are mostly used for industrial or non-residential construction. The presence of stiffening ribs provides the finished building with high resistance to all kinds of influences, but due to the uneven surface on the ceiling, they will look unaesthetic.
To level the surface, you will have to spend a lot of money and materials. When laying out, floor slabs can be laid with the ribs up, forming a trough, but more often the installation occurs in the traditional way - with the ribs down. In accordance with the standards, the following dimensions are characteristic for products:
- height - 40 and 30 cm (for prestressed slabs);
- length - 5-5.5 m;
- width - 0.74-2.985 m.
The main advantages of using (in terms of construction) ribbed floor slabs is the ability to erect a building in the temperature range from -40 to + 50 °, as well as the ability to resist when exposed to seismic activity equal to 9 points.
The final stage in the construction of any building is considered to be the design of the attic and the roof. For this, special coating panels are used, after the installation of which the roof is erected using finishing materials such as bitumen or liquid rubber, which perform a waterproofing function and at the same time are distinguished by a low cost.

The main areas of application of ribbed slabs are industrial buildings and utility rooms for various purposes.
Cover plates are mounted in a standard or ribbed way. To improve the durability of the structure, stressed reinforcement is used. This type of slab is distinguished by its ability to withstand increased loads up to 1500 kg / m². In the structure of the slab, embedded elements made of steel reinforcement are used, which are connected to adjacent parts. Among the most popular sizes, there are such options:
- width - 2-3 meters;
- length - 6-12 meters;
- thickness varies from 250 to 455 mm.
Concrete wall slabs were designed to speed up the construction of a building, for example, a slab house can be completed in just 2-3 weeks. Among the main types are the following:
- Single layer. They are made from a homogeneous concrete mixture with low thermal conductivity. Their thickness does not exceed 4 cm.
- Two-layer. The load-bearing inner layer is made with reinforced concrete, and the outer one is made with cement-sand mortar.
- Three-layer. They are performed by combining the first two types of slabs, for which a welded reinforcement cage is used. A layer of insulation is usually added between the layers.
It is interesting! Depending on the bearing capacity, wall slabs are hinged, self-supporting and load-bearing.
A separate group can be divided into slabs for partitions, which are distinguished by large dimensions corresponding to the height of the floors. The length of such concrete structures is usually 6 meters.For the manufacture of panels, ordinary or gypsum concrete of increased strength is used, which is characterized by good water and frost resistance. The thickness of the wall slabs should be selected according to the weather conditions in the region. Depending on the requirements, panels with a thickness of 20-50 cm are manufactured.
Other options for concrete products used for various purposes
When building roads, special road concrete slabs are used, in the production of which high-strength concrete of the B-25 or B-30 grade is used. A distinctive feature of these concrete products is considered to be resistance to tensile bending. It is this characteristic that ensures the durability and high carrying capacity of highways. Concrete paving slabs, which were made with reinforced reinforcement, can be installed when creating runways designed for increased loads. The main characteristics of the products:
- the ambient temperature range at which it is permissible to use the products without losing their properties is from -55 to +40 ° С;
- abrasion index - 0.7 g / cm²;
- frost resistance class - F250.
Depending on the configuration, road slabs are rectangular, trapezoidal or hexagonal. It is important to bear in mind that the base must be properly prepared before laying concrete slabs. For this, the top soil layer is removed and leveled, and the site for laying is well rammed. Then a pad of wet sand is poured, which is compacted with a roller, and only then can the slabs be placed. The cavities between the slabs are filled with quality concrete.
Concrete slabs for paths and sidewalks are produced by vibrocasting or vibrocompression. After the product has been given the desired shape and size, the tiles go through a steaming stage until the complete crystallization of the concrete mixture occurs. The color of the tiles is given by adding natural impurities, so that they do not fade and do not wear out over time. According to GOST standards, concrete paving slabs must have a single-layer or two-layer structure. It is the two-layer options that are distinguished by the presence of an upper decorative colored layer 2 cm thick.The main advantages of the products are:
- high wear resistance to mechanical damage;
- long service life;
- attractive appearance;
- easy assembly and disassembly;
- the presence of only natural materials in the composition.
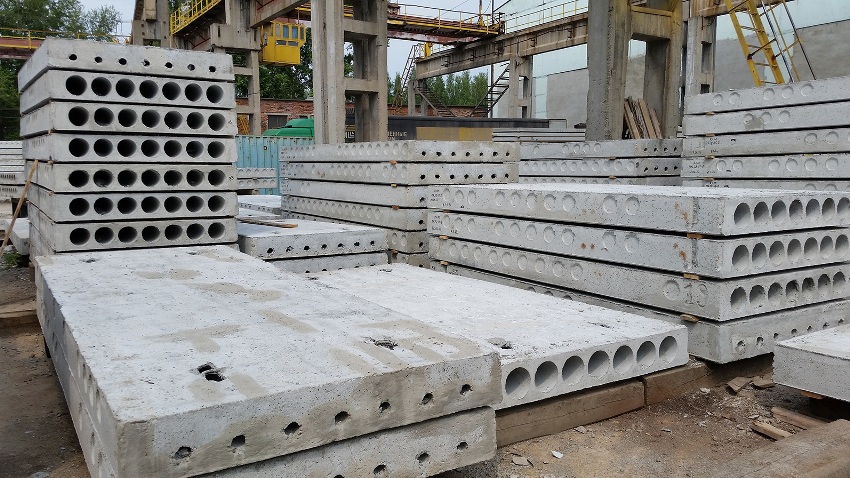
The durability and reliability of structures is directly dependent on the quality of the concrete materials themselves.
In addition to the listed products, concrete is also used for the manufacture of other elements, such as:
- Fences. Monolithic concrete slab fence cast directly on the site using formwork. This version of the fence is distinguished by the simplest installation method. There are also concrete euro- and type-setting fences, which are characterized by a variety of colors and shapes.
- Well ceiling slabs. These are reinforced concrete floor slabs with pre-prepared holes for the hatch, marked with PP. The variety of sizes allows the use of concrete covers designed for wells of various diameters.
The first concrete slab was made more than a century ago, and since then the products have been constantly modernized. This not only improves their appearance, but also increases the load capacity of the products. Manufacturers compete to create the lightest board possible while maintaining its dimensions and properties. In general, concrete panels are considered to be an excellent building material, allowing you to quickly create a reliable and stable structure. The main thing is to choose the right size and type of plate.